Comprehensive Guide to Precision Instrumentation Applications, Types, and Latest Developments
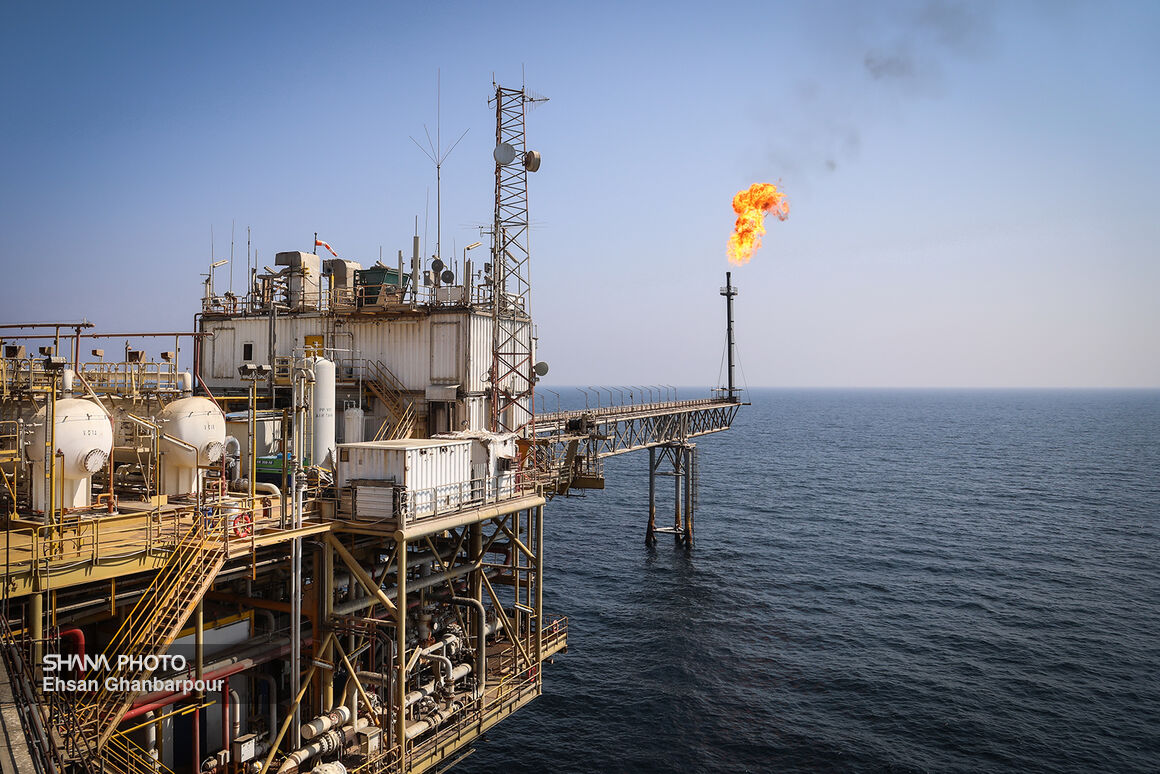
What is Instrumentation?
Instrumentation refers to devices and equipment designed to measure and control various parameters in industrial and laboratory processes. These tools are essential for their high precision and ability to measure physical or chemical variables with great accuracy. They are widely used in industries such as automotive, oil and gas, pharmaceuticals, and biomedical engineering.
Types of Instrumentation
Instrumentation can generally be divided into two categories:
- Measurement Instruments: These tools are used to measure different parameters like temperature, pressure, humidity, flow, and level. Examples include thermometers, pressure gauges, and flow meters.
- Control Instruments: These devices are used to regulate and control processes or systems. Examples include control valves, regulators, and PID controllers.
Importance of Instrumentation
Instrumentation plays a crucial role in improving product quality and reducing errors in industrial processes. High precision in measurement and process control can lead to increased safety, cost reduction, and enhanced performance of industrial systems.
Applications
These instruments are used in various industries:
- Oil and Gas Industry: For measuring pressure, temperature, and flow of gases and liquids.
- Pharmaceutical Industry: For precise control of temperature and humidity in drug production.
- Automotive Industry: For measuring and controlling various car characteristics like tire pressure and engine temperature.
Digital Thermometers: Technology and Applications
Digital thermometers are precise instruments used for measuring the temperature of various substances. Compared to analog thermometers, these devices offer higher accuracy and can easily display temperatures in different units such as Celsius or Fahrenheit.
Types of Digital Thermometers
- Probe-Type Digital Thermometer: This type typically has a probe sensor that is inserted into or onto the surface of the measured substance. It is commonly used in food and medical industries.
- Infrared Digital Thermometer: This type can measure surface temperatures of objects from a distance without contact. Its primary application is in the automotive and electronics industries.
Advantages of Digital Thermometers
- High Accuracy: Digital thermometers generally offer more precision compared to analog models.
- Easy Readability: The digital display allows users to easily read the temperature.
- Fast Response Time: Digital thermometers usually have a quicker response time.
Applications
- Medical Industry: For measuring patients’ body temperature.
- Food Industry: For measuring cooking temperatures of food.
- Automotive Industry: For measuring engine and car parts temperature.
Pressure Sensors: Types and Applications
A pressure sensor is a tool designed to measure the pressure of gases or liquids in various systems. These sensors are used in different industries to monitor complex systems and ensure safe operation.
Types of Pressure Sensors
- Resistive Pressure Sensors: In these sensors, pressure changes cause variations in the electrical resistance of a specific material. They are used in low-temperature applications.
- Capacitive Pressure Sensors: In these sensors, pressure causes changes in capacitance. They are suitable for measuring highly precise pressures.
- Semiconductor Pressure Sensors: These sensors use semiconductor technology to convert pressure into an electrical signal, providing high accuracy.
Advantages of Pressure Sensors
- High Accuracy: These sensors typically have very high accuracy, which is crucial for sensitive applications.
- Long-Term Stability: Pressure sensors usually maintain their accuracy over time.
- Resistance to Harsh Conditions: Many pressure sensors are designed to operate reliably in harsh environmental conditions, such as high temperatures or extreme pressures.
Applications
- Oil and Gas Industry: Measuring pressure in pipelines and gas systems.
- Automotive Industry: Measuring pressure in brake and fuel systems.
- Medical Industry: Used in respiratory devices and blood pressure measurement.
Temperature Sensors: Functionality and Applications
Temperature sensors are precise tools designed to measure the temperature of various substances. These sensors come in different types and have extensive applications in industry and laboratories.
Types of Temperature Sensors
- Thermocouples: These sensors consist of two different metals that produce a voltage when the temperature changes. Thermocouples are suitable for measuring a wide range of temperatures.
- RTD (Resistance Temperature Detector): These sensors are made from specific materials whose resistance changes with temperature. RTDs have higher accuracy compared to thermocouples.
- Thermistors: These sensors are also made from semiconductor materials and are suitable for precise and limited temperature ranges.
Advantages of Temperature Sensors
- High Accuracy: Temperature sensors usually have high accuracy and are designed for precise temperature measurement in various conditions.
- Stability: Many temperature sensors have good resistance to environmental changes.
- Variety: Temperature sensors come in various types and are available for different applications.
Applications
- Oil and Gas Industry: Measuring the temperature of oil processes.
- Food Industry: Controlling the temperature during cooking and packaging of food.
- Pharmaceutical Industry: Monitoring the temperature in drug production processes.
Calibration of Instrumentation: Why and How?
Calibration is a process where precision instruments are adjusted to ensure their accuracy. This process is especially important in sensitive industries such as pharmaceuticals, automotive, and aerospace.
Importance of Calibration
- Accuracy: Calibration helps maintain measurement accuracy.
- Compliance with Standards: Many industries have international standards that precision instruments must be calibrated according to.
- Safety: In some industries, measurement errors can lead to safety hazards, making regular calibration essential.
Calibration Process
Calibration is usually done by comparing precision instruments with known standards. This process can be performed manually or automatically and requires specialized equipment.
Applications
- Pharmaceutical Industry: Ensuring measurement accuracy in drug production.
- Automotive Industry: Calibrating measuring instruments for producing safe vehicles.
- Laboratories: Ensuring the accuracy of test results.
History of Instrumentation: From Inception to Today
Instrumentation has been an integral part of human civilization since the time people began measuring and controlling environmental factors. Over time, these instruments have undergone significant transformations with scientific and technological advancements, becoming a crucial component of various industries today.
Early Use of Precision Instruments
The earliest precision instruments date back approximately 400 years. During that time, basic devices were used to measure time and length. The first clocks, compasses, and rudimentary tools for measuring temperature and pressure emerged during the Renaissance. These instruments still form the foundation of many modern technologies.
Advances in the 19th and 20th Centuries
In the 19th century, scientific breakthroughs like the discovery of new physical laws and advancements in manufacturing technologies led to the development of more complex instrumentation. The invention of advanced thermometers, pressure gauges, and precise measuring machines significantly transformed industries. These instruments not only provided accurate measurements but also enabled measurements on a larger scale with much higher precision.
Digital Revolution and Instrumentation in the 21st Century
With the advent of digital technology in recent decades, instrumentation has reached a new level of accuracy and efficiency. The use of microcontrollers, sensors, and Internet of Things (IoT) systems has guided the industry towards the future. Instruments that can now transmit various data online and automatically adjust and control settings demonstrate significant advancements in precision and efficiency.
The Future of Instrumentation
Today, precision instruments play a vital role in all industries, from automotive and aerospace to medicine and energy engineering. Especially with the growth of technologies such as artificial intelligence and machine learning, it is expected that precision instruments will become even smarter and more self-regulating in the near future.
Latest Developments in the World of Instrumentation: Advances and Innovations
In today’s world, instrumentation plays a crucial role in controlling industrial, medical, scientific processes, and even in daily life. With technological advancements and the increasing demand for higher accuracy, new developments in this field have emerged that could revolutionize the future of the industry.
1. Internet of Things (IoT) and Instrumentation
One of the most significant recent developments in the world of instrumentation is its integration with the Internet of Things (IoT). IoT means that precision instruments are capable of sending data online to other devices and systems. This improves monitoring and control processes and can aid in automation and predicting issues before they occur.
2. Use of Artificial Intelligence and Machine Learning
Artificial intelligence and machine learning are increasingly being utilized in the world of instrumentation. These technologies can analyze data collected by precision instruments and identify hidden patterns and trends. These advancements enhance predictions, optimize processes, and reduce errors. For example, in the automotive industry, cars can automatically adjust engine settings according to different conditions.
3. Smart Sensors
Smart sensors, which combine precision sensors and data processing systems, have recently entered the market. These sensors can analyze data independently and process information in real-time. Smart sensors are used in the medical, automotive, agricultural industries, and even in smart homes.
4. Portable and Affordable Precision Instruments
Another interesting advancement in instrumentation is the reduction in cost and size. Portable precision instruments, which were previously only used in complex and specialized industrial environments, are now widely available to the public. This advancement in cost and size has made it possible to use these instruments in homes and small businesses.
5. The Use of Nanotechnology
Nanotechnology has become a tool that enables the creation of precision instruments with microscopic accuracy. This technology can be revolutionary, especially in the fields of medicine and scientific research, by providing precise instruments with new capabilities. For example, nanosensors can be used for early detection and prediction of diseases.
The Future of Instrumentation: Towards a Smarter World
Given the rapid advancements and novel technologies, the future of instrumentation will dramatically change. It is expected that precision instruments will not only have greater accuracy and efficiency but also possess smarter capabilities for process control and problem prediction. Additionally, with unprecedented advancements in the IoT and big data domains, precision instruments in the future could manage industrial and scientific processes entirely autonomously, without human intervention.